On the threshold of fossil-free steel production
We are poised for the greatest single technological shift that the global steel industry has ever seen. With the help of hydrogen and a transformation of the entire value chain from extraction to end-product, the industry now has an historic opportunity to enable the global climate transition. For Sweden, this also offers a significant jump in exports.
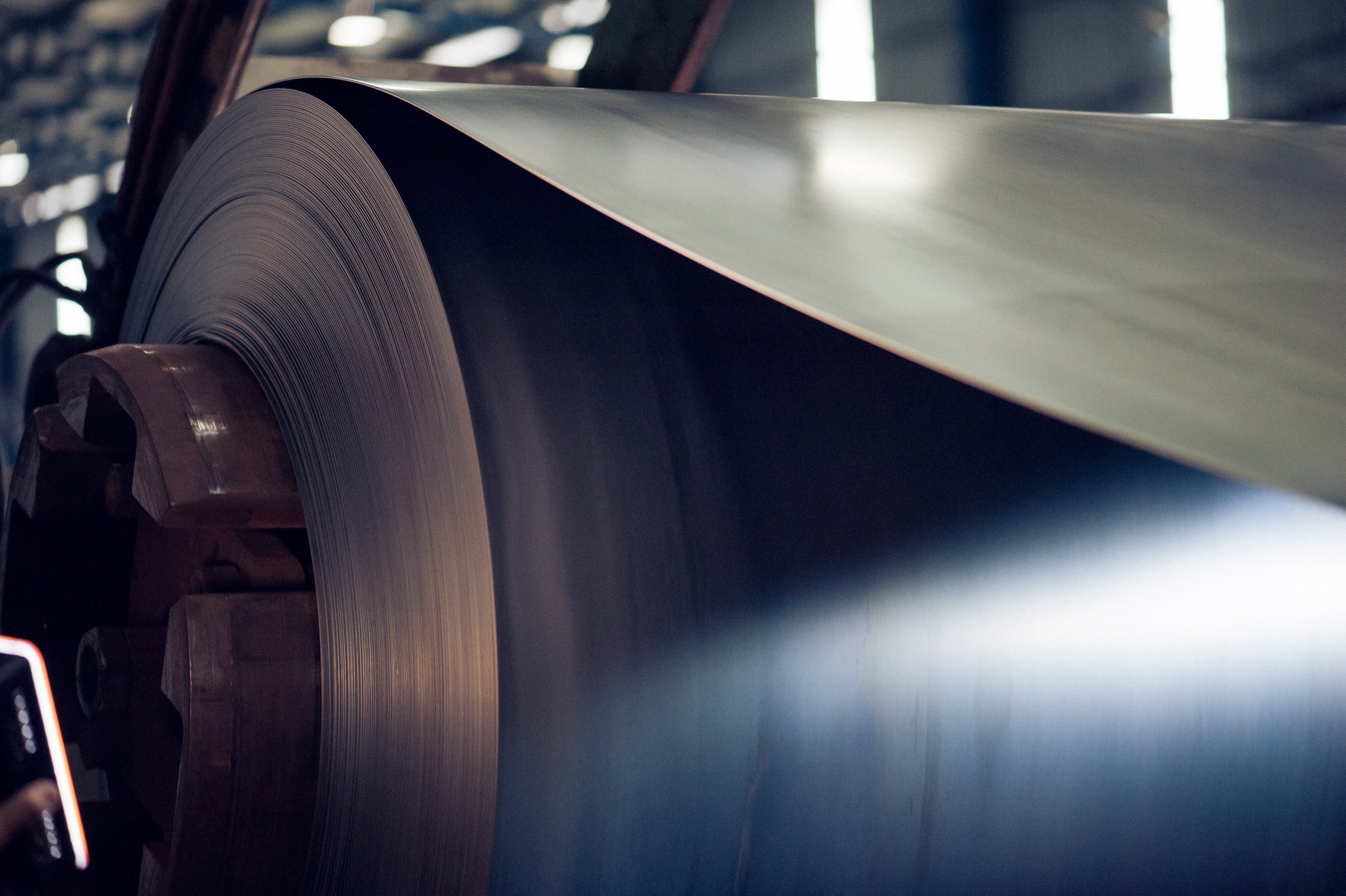
Steel is one of the most important industrially produced materials – and a key component of modern society. It is used in the construction and automotive industries, in the manufacture of electronics and white goods, and in many other applications. At the same time, the steel industry is one of largest carbon dioxide emitters, accounting for six percent of carbon dioxide emissions in the EU and seven to nine percent of global carbon dioxide emissions. It is therefore vital that we succeed in removing carbon dioxide from steel production, (a process known as decarbonization).Decarbonization is now set to challenge old technology. Conventional steel production is based on the supply of coke and coal. We are now facing a paradigm shift: traditional blast furnace-based technology is being replaced by direct reduction, where hydrogen is used instead of coal and coke. This results in steam being the only by-product and we reduce carbon emissions.All around the world, research programs, pilot projects, and development initiatives are currently focusing on accelerating this transformation. However, this transformation will not happen by itself. The traditional steel industry is located in the wrong places and has made major investments in old technology. Change requires substantial investment from an industry that is capital-intensive but has small margins. The transition also requires access to cheap renewable energy, which is a challenge.To achieve the change, we need to build from scratch, on a large scale and with vertical integration. Sweden offers unique opportunities for green steel production, with good access to fossil-free electricity, the best quality iron ore in Europe, and a specialized and innovative steel industry. Fossil-free electricity and its conversion to hydrogen are key components. It therefore makes sense that we are based in Norrbotten, northern Sweden, close to such energy sources. The HYBRIT Project has inspired us. And we envisage close collaboration with business, the public sector, and Luleå University of Technology in particular, where we are now building our business.In this context, the development of hydrogen is vital. So-called green hydrogen, which is produced using electricity, has rapidly become an energy solution that is attracting considerable investment as society quickly takes steps to achieve climate goals. In addition to the role that hydrogen will play in steelmaking, hydrogen can also replace fossil fuels in industry, aviation, truck transport, and cogeneration. In addition, it can be used to store electricity from solar and wind power. The European Commission has presented a hydrogen strategy that will make Europe a leader in the segment. It is estimated that up to EUR 470 billion, approximately SEK 5,000 billion, will be invested in the transition.The Swedish steel industry currently produces approximately 4.7 million tons of steel annually and is therefore a relatively small player in the global market. Iron ore from Sweden is shipped to other countries. With our experience and our learnings from Northvolt of quickly building a completely new industry, we have developed a roadmap that makes it possible to build the world’s first large-scale green steel production facility – with the goal of producing five million tons of steel by 2030. In addition, the climate gains that this entails will also mean an increased net export value of around SEK 30 billion for the Swedish economy.Conventional steelworks across Europe are large and complex. They often transport large quantities of steel from one production plant to another before a final product is ready. This is inefficient in terms of energy use, transport, and storage. Therefore, greenfield investment is required – to build new facilities from scratch.That is why we’re creating a new, fully integrated steel producer, and implementing the latest technology at every step of the production process.By cutting costs at every step with automation digitization, a fully integrated production process, and access to energy from renewable energy sources, we will produce as many as five million tons of green steel by 2030. A goal also supported by building on lessons learned from our Northvolt journey, our foundry model, and by developing the company in close collaboration with customers, investors, and technology partners.