How Digitalization Will Enable Completely Different Ways of Working in Steelmaking
Despite its ubiquity in society and other industries, digital technologies have only begun to penetrate the steel industry. Steel workers have traditionally relied on their gut instinct, or intuition, to make important decisions, based on years of experience with information handed down from one generation to the next.
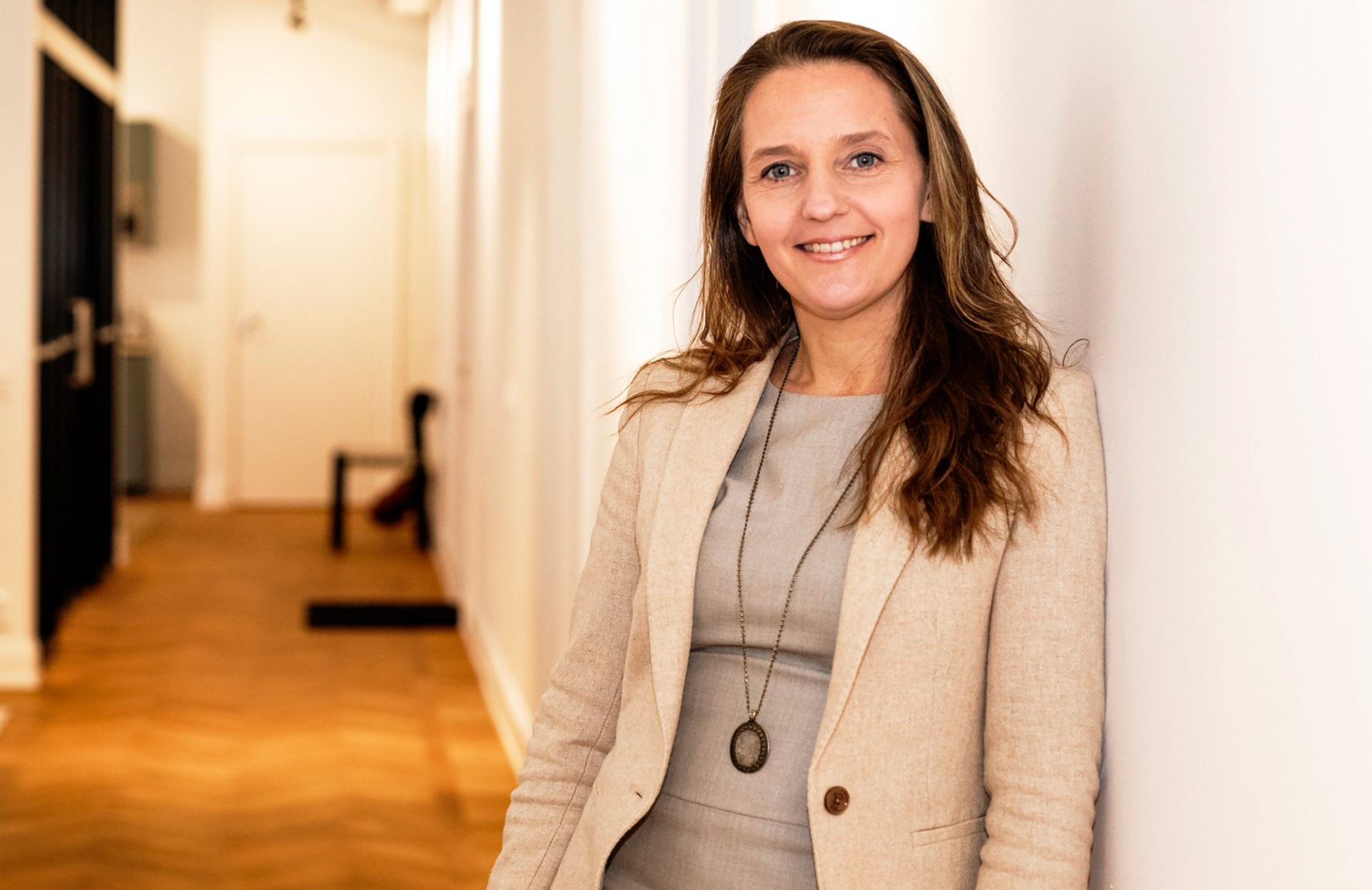
“The steel workforce is coming of age, and we are not adding enough apprentices or trainees to preserve knowledge legacies. An operator who has been in the industry for 40 years has a unique ability to sense when parameters are off – and when they are perfectly aligned,” says Maria Persson Gulda, Chief Project Officer and Chief Technology Officer at H2 Green Steel.Today, technology, automation and digital record-keeping and tracking allows us to make reliable data-driven decisions – without having to gut-check them, she says. “The gut feeling is so difficult to concretely explain from an operational point of view because the parameters in steel production are too complex for the human brain to interpret. Machine learning and artificial intelligence enables us to create tools that can process large amounts of data and connect the dots.” Her colleague Olof Hernell, Chief Digital Officer at H2 Green Steel, agrees. He highlights that it’s their cross functional teams – where experiences from material science and data science are combined – that will create the greatest value, with the common goal of revolutionizing the steel industry. “At H2 Green Steel, we do not draw a line between the physical and the digital world. Fully integrated teams – that’s our secret sauce,” he says. Maria and Olof shared how digitalization will improve quality assurance in steel production, and its future potential impact on everything from operations and the role of steel engineers to mechanical property and safety.
The metal industry lags behind other industries on digital maturity – why is that?
H2 Green Steel is embarking on new ground, but are there predecessors or others who have inspired your digital best practices?
What value does digitalization add to steel production?
Finally, what is the impact on safety?